More Client Reference




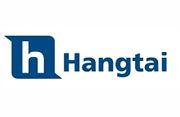



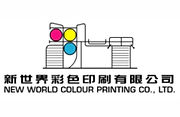


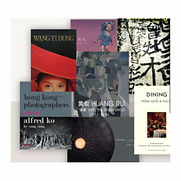
iTTG > Industry Solutions > Printing and Packaging Industry
Companies in the printing and packaging industry face a unique set of challenges, navigating through rapid shifts in consumer preferences and environmental regulations. This sector demands constant innovation in materials and processes to deliver sustainable, high-quality packaging solutions. Additionally, the integration of digital technologies for personalized packaging and streamlined production processes is essential. Managing these dynamics effectively is crucial for staying competitive and meeting the evolving needs of the market.
How to start?
Need help?
iTTG Hotline: (60) 4 222 8926
​
Hotline Service Hours:
Monday to Friday 9:00 am – 5:00 pm
Key Industry Challenges for the Industry
-
Is Epicor’s cloud accounting system used in Malaysia?Absolutely! Epicor’s cloud accounting system is widely adopted by Malaysian businesses due to its flexibility and scalability. At iTTG, we customize Epicor to align with your business workflows, ensuring full integration of financial data and processes across different departments, such as sales, purchasing, inventory, and warehousing—all securely managed in the cloud.
-
How long does it typically take to implement Epicor ERP?Implementation time varies depending on your business size and complexity. However, with iTTG Consultancy's expertise, most small to mid-size manufacturers can expect full implementation within 3-6 months. We'll provide a more accurate timeline after assessing your specific needs.
-
What kind of return on investment (ROI) can we expect from implementing Epicor ERP?While ROI varies, many of our clients report significant improvements within the first year. These include reduced operational costs, increased productivity, better inventory management, and improved financial accuracy.
-
What is a cloud-based accounting system?A cloud-based accounting system is an online platform hosted remotely, allowing multiple users to access, update, and manage all financial data in real time. This ensures data accuracy and provides a clear, up-to-date view of financial status. With a cloud-based accounting system, businesses can streamline and automate their financial processes, reducing mundane data entry and minimizing human errors.
-
Is Epicor cloud accounting system available for e-invoicing in Malaysia?Yes! At iTTG, we customized the e-invoicing feature in Epicor’s cloud accounting system, specifically designed for Malaysian businesses of all sizes and industries. We ensure the e-invoice solution meets the regulatory requirements set by LHDN, allowing businesses to submit invoices to the LHDN portal with a single click. Send us your inquiries today!
-
How can Epicor ERP improve financial management processes?Epicorcloud ERPstreamlines your financial operations by automating key processes, providing real-time data visibility, and integrating all financial aspects of your business. This leads to improved accuracy, faster reporting, better cash flow management, and more informed decision-making.
-
What training does iTTG Consultancy provide for our team during and after implementation?We offer comprehensive training programs tailored to different user roles within your organization. This includes hands-on system training, process workshops, and documentation. Post-implementation, we provide ongoing support and additional training as needed to ensure your team maximizes the benefits of Epicor ERP.
-
How does Epicor WMS enhance labor efficiency in Malaysia?With features like automated pick-pack-ship processes, Epicor WMS helps minimize manual labor dependencies, reduce human errors, and enhance overall worker productivity in warehouses in Malaysia.
-
What are the key benefits of implementing WMS for businesses in Malaysia?Implementing WMS helps Malaysian businesses enhance warehouse efficiency by optimizing inventory management, streamlining order processing, maximizing space utilization, and accurately tracking goods across the supply chain. This leads to reduced costs, improved customer satisfaction, and better decision-making.
-
What's the difference between WMS and ERP?WMS: A standalone system focused solely on optimizing warehouse operations like inventory management and order fulfillment. It lacks of additional functionality of an ERP system ERP: An all-in-one business solution that centralizes multiple functions, including warehouse management, sales, purchasing, finance, and more into one single platform, providing comprehensive operational oversight and streamlined data flow across departments. With Epicor ERP’s integrated WMS tailored to the needs of Malaysian businesses, iTTG ensures that warehouse operations are streamlined from stock receiving to delivery.
-
What is a Warehouse Management System (WMS)?A WMS, or warehouse management system, is a software application designed to manage and optimize warehouse operations in Malaysia. It helps organizations control and track the movement and storage of materials within a warehouse, from receiving to shipping, ensuring efficient operations and inventory accuracy.
-
What is ERP Software?ERP, or Enterprise Resource Planning, is a software system in Malaysia that integrates core business processes and functions into a unified platform. It allows organizations to manage and automate various aspects of their operations, including finance, human resources, manufacturing, supply chain, and customer relationship management. ERP software systems enable businesses in Malaysia and around the world to streamline workflows, improve data accuracy, and make informed decisions based on real-time information.
-
What services does iTTG Consultancy offer?iTTG Consultancy offers a wide range of services, including ERP software consultation, implementation, and support, with a special focus on Epicor ERP systems. As Epicor ERP consultants in Penang, we provide tailored solutions for warehouse management, supply chain optimization, and cloud accounting systems.
-
Why choose Epicor ERP?Epicor ERP software is known for its flexibility, scalability, and ability to support complex business processes. It is designed to enhance productivity, streamline operations, and improve overall efficiency, making it an ideal choice for businesses looking to optimize their operations and drive growth.
-
How can I make an appointment with iTTG Consultancy?To make an appointment with iTTG Consultancy, simply contact us through our website, email, or phone. Our team will schedule a consultation at your convenience to discuss your business needs and how we can help you achieve your goals. Visit our Penang branches for in-person consultations.
-
Why should I hire a Cloud ERP consultant?Hiring a Cloud ERP consultant brings specialized expertise and guidance to ensure successful implementation and optimization of your ERP system in the cloud. Consultants like those at iTTG can assess your business needs, recommend the right cloud ERP solution, customize it to fit your requirements, and provide ongoing support and training. We also streamline the migration process from on-premises systems to the cloud, ensuring minimal disruption to your operations while maximizing the benefits of cloud technology.
-
Is Cloud ERP secure?Yes, reputable Cloud ERP providers implement stringent security measures to protect data. This includes encryption protocols, secure access controls, regular security audits, and compliance with industry standards and regulations. Data stored in the cloud is often more secure than on-premises solutions due to dedicated security teams and advanced infrastructure.
-
How to connect with Epicor cloud ERP consultant?To get in touch with an Epicor Cloud ERP consultant at iTTG, you can reach out through email or website contact form. Our cloud ERP consultants will get back to you shortly. Whether you need advice on Epicor ERP implementation, customization, or support, our expert consultants are here to help you optimize your business operations.
-
What is Cloud ERP?Cloud ERP (Enterprise Resource Planning) is a software solution that allows businesses to manage their core operations such as finance, human resources, manufacturing, and supply chain management through the cloud. It eliminates the need for on-premises hardware and infrastructure, offering flexibility, scalability, and accessibility from anywhere with an internet connection.
-
What are the benefits of Cloud ERP?Cloud ERP offers several advantages, including reduced upfront costs, lower maintenance expenses, automatic software updates, enhanced security protocols managed by the provider, scalability to accommodate business growth, and real-time data accessibility for improved decision-making and collaboration. Watch video: What are the benefits of ERP
-
What is the difference between Cloud ERP and traditional ERP?Cloud ERP: Deployment: Hosted on remote servers, accessed via the internet. Cost: Subscription-based, lower upfront costs, reduces IT overhead. Accessibility: Offers remote and mobile access, scalable on-demand. Maintenance: Vendor-managed updates, reduces internal IT burden. Security: Shared responsibility, robust measures by providers. Traditional ERP: Deployment: Installed locally on company servers, on-premises. Cost: Higher initial investment in hardware, licenses, and IT infrastructure. Accessibility: Limited to on-site access, scalability may require more investment. Maintenance: Internally managed updates, requires dedicated IT resources. Security: Relies on internal IT team for implementation and upkeep.
-
Epicor Project ManagementThe Epicor Project Management function offers substantial advantages to Automotive Part factories by enhancing project organization, resource allocation, and cost control. Utilizing Work Breakdown Structure (WBS) or Milestones, it enables precise task allocation and progress tracking, ensuring efficient project execution. This structured approach aids in managing resources effectively, adhering to budgets, and preventing cost overruns. Additionally, close monitoring of costs at various project stages facilitates financial oversight, contributing to improved profitability. Integration with Microsoft Office Project enhances collaboration and adaptability, further optimizing project management processes. Overall, Epicor Project Management streamlines operations, leading to enhanced efficiency and profitability for Automotive Part factories.
-
Inventory Inaccuracy and Resource ConstraintsInaccurate inventory tracking and an inability to efficiently manage resources can result in stockouts, excess inventory, write-offs, and ultimately, financial losses.
-
Missed Revenue and Opportunity Expansion in Field ServiceFailure to capitalize on revenue-generating opportunities during field service can result in missed sales, underutilized resources, and an inability to fully leverage customer relationships for business growth.
-
Inefficient Sheet Metal Fabrication and Inventory OptimizationPoor management of sheet metal dimensions and stock can lead to material wastage, increased costs, and inefficiencies in production processes.
-
Failure to Transition to a Paperless Shop FloorNot moving towards paperless operations can lead to inefficiencies, higher operational costs, increased error rates, and environmental impacts, hindering process optimization and sustainability efforts.
-
Lack of Real-Time Product Cost MonitoringWithout real-time monitoring and control of product costs, companies may face reduced profit margins, an inability to make informed pricing decisions, and challenges in responding to market price pressures.
-
Field Engineer Productivity and Customer Satisfaction IssuesInsufficient support for field engineers can decrease on-site efficiency and customer satisfaction, impacting service quality and potentially leading to a decrease in repeat business and referrals.
-
Complexity in Product Structures and Documentation ManagementFailing to manage complex product structures and associated documents efficiently can result in errors, increased time to market, and challenges in maintaining compliance and quality standards.
-
Dynamic Design Changes and Inefficient Job SchedulingNot adapting quickly to design changes or efficiently rescheduling jobs can lead to production delays, increased costs, and an inability to meet customer delivery expectations.
-
Lifecycle Cost Management InefficienciesPoor control over the product lifecycle costs can lead to budget overruns, delayed product launches, and diminished profitability, affecting overall market competitiveness.
-
Challenges with Diverse Manufacturing MethodsInability to effectively manage different manufacturing methods can cause production inefficiencies, increased waste, and higher costs, leading to decreased operational flexibility and market responsiveness.
-
Ineffective Customer Interaction and Quality ManagementInadequately managing customer inquiries and complaints can lead to decreased customer satisfaction and loyalty, negatively impacting brand reputation and long-term revenue potential.
-
Inaccuracies in Cost Estimation and QuotationFailure to provide accurate and timely quotations can result in lost sales opportunities, customer dissatisfaction, and a tarnished reputation in the marketplace.
-
Epicor MESManufacturing Execution Systems (MES) can significantly benefit a machinery factory by providing real-time monitoring and control over production processes. By integrating MES, factories can track the progress of manufacturing orders, monitor the performance and availability of machines, and ensure that quality standards are met throughout the production cycle. This system enhances operational efficiency by minimizing downtime, reducing waste, and optimizing resource utilization. MES also supports decision-making with data-driven insights, enabling managers to identify bottlenecks, improve production schedules, and adjust workflows promptly. Furthermore, it facilitates compliance with industry standards and improves traceability, ensuring that every product meets the required specifications. Ultimately, MES empowers machinery factories to achieve higher productivity, improved quality, and increased competitiveness in the market.
-
Epicor Project ManagementEpicor Project Management offers significant advantages to a machinery factory, enhancing efficiency and cost control for large-scale manufacturing projects. By employing Work Breakdown Structure (WBS) or Milestones, it enables detailed project organization, facilitating precise task allocation and progress tracking. This structured approach aids in effectively managing resources and adhering to budgets, crucial for operational success. The capability to monitor costs closely at various project stages ensures financial oversight, preventing overruns. Additionally, the feature supports non-manufacturing project management and integrates with Microsoft Office Project, improving project adaptability and collaboration. This comprehensive tool set streamlines project execution, leading to better outcomes and increased factory profitability.
-
Epicor Mobile Field ServiceA Mobile Field Service system offers substantial benefits to a machinery factory with field engineers providing onsite services. It enhances service efficiency by enabling real-time communication between field engineers and the central office, allowing for instant access to work orders, customer information, and technical documentation. This immediacy improves response times to service calls and enables on-the-spot diagnosis and resolution of issues. Inventory management features ensure engineers have the necessary parts and tools, reducing return visits. GPS tracking optimizes route planning, saving time and fuel. Moreover, the system facilitates immediate billing and feedback collection, enhancing customer satisfaction. By streamlining field operations, the factory can achieve greater productivity, reduced operational costs, and improved service quality, leading to increased customer loyalty and revenue.
-
Epicor CRMThe Epicor Customer Relationship Management (CRM) function offers a machinery factory a comprehensive toolset to enhance its customer acquisition and retention strategies. By facilitating the creation and tracking of marketing campaigns, it enables the factory to identify and target prospects effectively, transforming them into satisfied customers. The CRM's lead management system streamlines the sales process, from initial contact to final order, ensuring a seamless transition through various sales stages. Sales personnel can manage prospects efficiently, thanks to features like workflow, forecasting, and the Salesperson Workbench. This leads to improved sales territory management and accurate sales forecasts. Overall, the CRM function optimizes the prospect-to-customer lifecycle, fostering better customer relationships and driving sales growth.
-
Mixed Mode ManufacturingEpicor mixed-mode manufacturing design offers substantial benefits to a machinery factory operations. It enables seamless integration of Make-to-Stock (MTS), Make-to-Order (MTO), and Engineer-to-Order (ETO) production modes within a single ERP system. This flexibility ensures that the factory can efficiently handle standard, customized, and highly specialized machinery production. Epicor ERP provides robust tools enable real-time visibility into customer orders, inventory levels, and production schedules, facilitating dynamic decision-making to meet varying demands. By optimizing resource utilization, reducing lead times, and improving order accuracy, the mixed-mode manufacturing design enhances operational efficiency, cost control, and customer satisfaction. It empowers machinery factories to thrive in a competitive market by delivering products tailored to customer needs while maintaining cost-effectiveness.
-
Epicor Engineering ManagementThe Epicor Engineering Management function can significantly benefit a machinery factory by enhancing the precision and adaptability of its manufacturing processes. Through accurate definition of components, subassemblies, and operations, it allows for the creation of detailed bills of materials and routings, forming a comprehensive method of manufacturing. As manufacturing practices evolve, the system's ability to update these methods ensures continuous alignment with production advancements. Part revision management, supported by Engineering Change Orders (ECO), facilitates controlled updates and approvals for changes, promoting quality and consistency. Additionally, the capability to engineer alternate methods for part revisions enables customization and flexibility across different manufacturing sites, optimizing production efficiency and responsiveness to specific requirements.
-
Epicor Mobile WarehouseEpicor Mobile Warehouse provides significant benefits to a machine production factory by modernizing and optimizing warehouse management. With this solution, workers can access real-time inventory data, track materials, and streamline warehouse operations directly from mobile devices. Barcode scanning enhances accuracy and efficiency, reducing errors in material handling and order processing. By enabling quick and accurate inventory updates, order picking, and shipping, it enhances productivity and order fulfillment speed. Additionally, it improves visibility into inventory levels, enabling better demand forecasting and inventory control. Overall, Epicor Mobile Warehouse empowers the factory to operate with increased efficiency, reduced costs, and enhanced customer satisfaction.
-
Epicor APSThe Epicor Advanced Planning & Scheduling (APS) function offers transformative benefits for a machinery factory by integrating comprehensive scheduling insights and tools. By accounting for variables like production quantities, setup times, and resource capacities, APS enables precise scheduling and job completion forecasting. Its visual boards and What If Scheduling tool allow for proactive adjustments, ensuring optimal resource allocation and preventing production bottlenecks. This leads to streamlined operations, improved efficiency, and reduced lead times. Moreover, analytical reports provide critical data on resource load and job prioritization, empowering decision-makers to enhance scheduling strategies. Ultimately, APS fosters a more agile, responsive, and efficient manufacturing process, directly contributing to increased productivity and customer satisfaction.
-
Epicor Product ConfigurationThe Epicor Product Configuration function can greatly benefit a machinery factory by streamlining the customization process for Make-to-Order (MTO) products. By utilizing the Configurator Designer, the factory can efficiently manage and offer a wide array of product customizations, from colors to sizes and hardware features. This tool simplifies the sales order entry, enabling accurate capture of customer-specific requirements and ensuring precise manufacturing instructions. It enhances operational efficiency by reducing errors in production planning and material sourcing. Additionally, the automated validation of configured part numbers against predefined rules minimizes manual intervention, ensuring compliance with design standards and accelerating the order-to-production cycle.
-
Epicor Real Time CostingEpicor Real-Time Costing provides significant benefits to a machine production factory by offering immediate visibility into the costs associated with manufacturing processes. This system enables the factory to track and analyze expenses as they occur, allowing for more accurate and timely financial reporting. By understanding the exact cost implications of raw materials, labor, and overheads in real-time, managers can make informed decisions to optimize production efficiency and reduce waste. This proactive approach to cost management helps identify profitability challenges early, facilitating swift adjustments to pricing strategies or operational practices. Ultimately, Real-Time Costing empowers a factory to improve its cost control, enhance competitive pricing, and boost overall profitability through precise and dynamic financial oversight.
-
Scheduling and Machine Optimization IssuesThe need to efficiently schedule and optimize the usage of printing machines, especially when multiple job orders compete for the same resources, presents a crucial operational challenge. This issue is pivotal to avoiding bottlenecks and ensuring timely production.
-
Lack of Real-Time Product Cost MonitoringWithout real-time monitoring and control of product costs, companies may face reduced profit margins, inability to make informed pricing decisions, and challenges in responding to market price pressures.
-
Logistical Hurdles in Material TrackingMaintaining an accurate track of paper movement through the diverse stages of production is a logistical nightmare. The challenge of ensuring that each stack of paper is accounted for, and identifying its origin from specific pallets, complicates inventory management and operational efficiency.
-
Procurement and Supply Chain ConstraintsThe task of procuring paper in the necessary dimensions and quantities is a critical challenge that affects production efficiency, cost control, and profitability. Precision in procurement and supply chain management is hampered by market variability and logistical complexities.
-
Complex Cost Estimation ChallengesThe process of accurately and swiftly estimating costs for quotations poses a significant challenge due to the intricate variables involved, such as paper and ink consumption, and the intricacies of prepress and postpress operations. This complexity often results in delays and inaccuracies that can impact competitiveness and profitability.
-
Ineffective Customer Interaction and Quality ManagementInadequately managing customer inquiries and complaints can lead to decreased customer satisfaction and loyalty, negatively impacting brand reputation and long-term revenue potential.
-
Rapid Response to Production ChangesThe printing industry's demand for short production lead times necessitates a system capable of quickly communicating changes and issues between the shop floor and production planning. The transition from traditional paper-based operations to more agile digital solutions is hindered by resistance to change and the challenges of implementing new technologies.
-
Die Cut Mold Management and Quality ConcernsEnsuring the quality and maintenance of die cut molds is a significant pain point. Effective management is essential, yet challenges in maintaining, storing, and procuring high-quality molds directly impact product quality and operational efficiency.
-
In-depth Cost Calculation DifficultiesAccurately capturing the actual cost of printed materials is fraught with difficulties due to the multitude of contributing factors such as paper consumption, machine usage, labor, and transportation costs. These costs, which accumulate throughout production and logistics, make it challenging to determine the true cost of printed matter.
-
Epicor Maintenance ManagementThe Epicor Maintenance Management function provides substantial benefits to Printing & Packaging factories by enhancing equipment reliability and optimizing maintenance processes. By tracking maintenance requests and scheduling preventative tasks for equipment like printing presses and packaging machinery, downtime is minimized, ensuring continuous production. The module allows for efficient management of capital equipment, tools, and fixtures, including air conditioning units and forklifts, critical for smooth operations. With predefined schedules and meter readings, maintenance tasks are performed promptly, reducing the risk of unexpected breakdowns. Overall, Epicor Maintenance Management empowers Printing & Packaging factories to maintain equipment reliability, minimize downtime, and optimize production efficiency, ensuring sustained operational excellence.
-
Epicor Cost Estimation & Quote ManagementThe Cost Estimation & Quote Management function offers significant benefits to Printing & Packaging factories by streamlining the process of generating accurate cost estimates and managing quotes efficiently. It allows for detailed breakdowns of costs, aiding in transparent pricing and ensuring competitiveness in the market. Additionally, seamless integration with other modules enables better coordination between quoting and production processes, improving overall operational efficiency. By enabling quick and accurate generation of quotes for both standardized and custom products, the module enhances customer satisfaction and facilitates better decision-making for resource allocation and pricing strategies.
-
Epicor Time ManagementThe Epicor Time Management function offers significant benefits to Printing & Packaging factories by streamlining labor tracking and management processes. Employees, managers, and supervisors can efficiently enter, approve, and correct time transactions, ensuring accurate recording of labor hours. With daily or weekly submission options, employees can easily submit their hours for approval, while authorized approvers can review and manage time entries promptly. This capability enhances payroll accuracy and compliance with labor regulations. Additionally, reports generated from the Time Management module provide valuable insights into employee work hours and utilization, enabling effective workforce management and optimization of production schedules in Printing & Packaging factories.
-
Epicor Job ManagementThe Epicor Job Management function offers substantial benefits to Printing & Packaging factories by streamlining manufacturing processes. It efficiently gathers data from various sources to create job records and define production schedules. With tools like the Job Manager and Planning Workbench, supervisors can effectively manage job creation and resource allocation. Labor costs are accurately tracked, and real-time status updates are provided through the Job Tracker. Key reports aid in job supervision, ensuring smooth operations from start to finish. Ultimately, Epicor Job Management enhances productivity, reduces errors, and improves overall efficiency in Printing & Packaging factories, leading to increased profitability and customer satisfaction.
-
Epicor CRMThe Epicor Customer Relationship Management (CRM) function offers significant benefits to Printing & Packaging factories by streamlining customer interactions and optimizing sales processes. By effectively managing leads and opportunities, the CRM facilitates targeted marketing campaigns, improving customer acquisition. Sales personnel can efficiently track prospects through various sales stages, ensuring seamless transitions from initial contact to final order. Features like workflow automation and forecasting enhance sales territory management and enable accurate sales forecasts. With comprehensive insights and analytics, the CRM empowers informed decision-making, driving revenue growth and fostering long-term customer relationships. Overall, it enhances efficiency, boosts sales performance, and strengthens customer engagement for Printing & Packaging factories.
-
Epicor APSThe Epicor Advanced Planning & Scheduling (APS) function offers significant advantages to Printing & Packaging factories by optimizing production planning and scheduling. By considering variables such as job quantities, setup times, and resource capacities, APS facilitates precise scheduling and forecasting of job completions. Its visual boards and What If Scheduling tool enable proactive adjustments, ensuring efficient resource allocation and preventing production bottlenecks. This results in streamlined operations, improved efficiency, and reduced lead times. Additionally, analytical reports provide critical insights into resource utilization and job prioritization, empowering decision-makers to enhance scheduling strategies. Ultimately, APS enhances agility, responsiveness, and productivity in Printing & Packaging manufacturing, driving customer satisfaction.
-
Epicor Project ManagementThe Epicor Project Management function offers substantial advantages to Printing & Packaging factories by enhancing project organization, resource allocation, and cost control. Utilizing Work Breakdown Structure (WBS) or Milestones, it enables precise task allocation and progress tracking, ensuring efficient project execution. This structured approach aids in managing resources effectively, adhering to budgets, and preventing cost overruns. Additionally, close monitoring of costs at various project stages facilitates financial oversight, contributing to improved profitability. Integration with Microsoft Office Project enhances collaboration and adaptability, further optimizing project management processes. Overall, Epicor Project Management streamlines operations, leading to enhanced efficiency and profitability for Printing & Packaging factories.
-
Epicor MESThe Epicor Manufacturing Execution System (MES) function offers substantial benefits to Printing & Packaging factories by providing real-time monitoring and control over production processes. Integration with MES enables tracking of manufacturing orders, monitoring machine performance, and ensuring quality standards throughout production cycles. This enhances operational efficiency by minimizing downtime, reducing waste, and optimizing resource utilization. Additionally, MES supports data-driven decision-making, allowing managers to identify bottlenecks, improve production schedules, and adjust workflows promptly. Moreover, it facilitates compliance with industry standards and enhances traceability, ensuring all products meet required specifications. Ultimately, Epicor MES empowers Printing & Packaging factories to achieve higher productivity, improved quality, and increased competitiveness in the market.
-
Epicor Real Time CostingEpicor Real-Time Costing offers substantial advantages to Printing & Packaging factories by providing immediate visibility into manufacturing expenses. This system allows real-time tracking and analysis of costs associated with raw materials, labor, and overheads, enabling accurate financial reporting and informed decision-making. With precise insights, managers can optimize production efficiency, reduce waste, and adjust pricing strategies accordingly. By proactively managing costs, Printing & Packaging factories can identify profitability challenges early and make swift adjustments to enhance competitiveness and overall profitability. Ultimately, Epicor Real-Time Costing empowers these factories to operate with heightened efficiency and financial transparency, ensuring long-term success in a dynamic market.
-
Epicor Mobile WarehouseEpicor Mobile Warehouse brings notable advantages to Printing & Packaging factories by modernizing and refining warehouse management. This solution grants real-time access to inventory data, enabling seamless material tracking and warehouse operations via mobile devices. Barcode scanning ensures accuracy and efficiency, minimizing errors in material handling and order processing. Swift inventory updates, order picking, and shipping enhance productivity and order fulfillment speed. Enhanced visibility into inventory levels aids in better demand forecasting and inventory control. Overall, Epicor Mobile Warehouse empowers Printing & Packaging factories to operate with heightened efficiency, reduced costs, and improved customer satisfaction, ensuring seamless warehouse management in a dynamic environment.
-
Lack of Real-Time Product Cost MonitoringWithout real-time monitoring and control of product costs, companies may face reduced profit margins, inability to make informed pricing decisions, and challenges in responding to market price pressures.
-
Difficult to Capture Production CostAccurately determining production costs in automotive part factories is challenging due to fluctuating raw material prices, varied labor costs, and complex manufacturing processes. Overhead allocation, mold and tool depreciation, and unexpected production issues further blur cost clarity. Advanced systems are vital for precise cost tracking and maintaining competitive pricing strategies.
-
Inefficient Sheet Metal Fabrication and Inventory OptimizationPoor management of sheet metal dimensions and stock can lead to material wastage, increased costs, and inefficiencies in production processes.
-
Scheduling and Machine Optimization IssuesThe need to efficiently schedule and optimize the usage of CNC machines, especially when multiple job orders compete for the same resources, presents a crucial operational challenge. This issue is pivotal to avoiding bottlenecks and ensuring timely production.
-
Rapid Response to Production ChangesThe Automotive Part industry's demand for short production lead times necessitates a system capable of quickly communicating changes and issues between the shop floor and production planning. The transition from traditional paper-based operations to more agile digital solutions is hindered by resistance to change and the challenges of implementing new technologies.
-
Procurement and Supply Chain ConstraintsMaterial procurement is a critical challenge that affects production efficiency, cost control, and profitability. Precision in procurement and supply chain management is hampered by market variability and logistical complexities.
-
Mold Management and Quality ConcernsEnsuring the quality and maintenance of molds is a significant pain point. Effective management is essential, yet challenges in maintaining, storing, and procuring high-quality molds directly impact product quality and operational efficiency.
-
Challenges with Diverse Manufacturing MethodsInability to effectively manage different manufacturing methods, for mold and molding production, can cause production inefficiencies, increased waste, and higher costs, leading to decreased operational flexibility and market responsiveness.
-
Ineffective Customer Interaction and Quality ManagementInadequately managing customer inquiries and complaints can lead to decreased customer satisfaction and loyalty, negatively impacting brand reputation and long-term revenue potential.
-
Why choose Epicor ERP Software in Malaysia?Epicor ERP software is known for its flexibility, scalability, and ability to support complex business processes in Malaysia. It is designed to enhance productivity, streamline operations, and improve overall efficiency, making it an ideal choice for businesses looking to optimize their operations and drive growth.
-
What services does iTTG Consultancy offer?ERP, or Enterprise Resource Planning, is a software system in Malaysia that integrates core business processes and functions into a unified platform. It allows organizations to manage and automate various aspects of their operations, including finance, human resources, manufacturing, supply chain, and customer relationship management. ERP software systems enable businesses in Malaysia and around the world to streamline workflows, improve data accuracy, and make informed decisions based on real-time information.
-
Which ERP Software in Malaysia is suitable for large enterprises?Large enterprises looking for scalability and streamlined operations may find Epicor better than any other ERP software in Malaysia due to its scalability, flexibility, and centralization features.
-
What is ERP software in Malaysia?ERP, or Enterprise Resource Planning, is a software system in Malaysia that integrates core business processes and functions into a unified platform. It allows organizations to manage and automate various operations, including finance, human resources, manufacturing, supply chain, and customer relationship management. Epicor is one of the best ERP software in Malaysia and around the world, which many businesses trust and choose. Epicor ERP software streamlines workflow, improves data accuracy, and makes informed decisions based on real-time information.
-
How can I make an appointment with iTTG Consultancy?To make an appointment with iTTG Consultancy, simply contact us through our website, email, or phone. Our team will schedule a consultation at your convenience to discuss your business needs and how we can help you achieve your goals.
-
How much does ERP Software cost in Malaysia?The cost of implementing ERP software in Malaysia varies depending on factors such as the modules you have chosen, the customization level, required enhancements, and the number of users. Our pricing is tailored to meet your business needs, combining subscription services with professional support. Contact us today for a personalized quote crafted just for you. Get your quote now!
-
How is ERP useful in the manufacturing industry?Implementing ERP software in the manufacturing industry can transform operations, drive business growth, and ultimately increase profitability. Here are some key advantages: Provides end-to-end visibility Improves operational efficiency Enhances inventory management Facilitates financial management Fosters collaboration between different departments For more information on the benefits of implementing manufacturing ERP software, please refer to this section.
-
What features should I look for in a manufacturing ERP system?Key features to consider in a manufacturing ERP system include: Cloud-based system Supply chain management Warehouse management Financial management Project management Customer relationship management (CRM) Enterprise performance management (EPM) Production planning and scheduling Inventory management Quality control Shop floor control Bill of materials (BOM) management Capacity planning Demand forecasting Real-time analytics and reporting Mobile accessibility Integration capabilities with other systems Compliance management Customisation options However, if you're uncertain which ERP features best suit your business needs, consider consulting ERP professionals like iTTG. These experts can provide valuable insights into ERP systems that align well with your manufacturing business requirements, helping you make an informed choice for your organisation's future.
-
What are the trends in the manufacturing ERP system?Here are some of the key trends in ERP software for the manufacturing industry nowadays: Adoption of Industry 4.0 technologies Smart manufacturing and the rise of customisation Sustainability and green practices Enhanced supply chain resilience Cloud-based ERP and remote operations Artificial intelligence and machine learning integration To learn more about these trends and innovations in manufacturing ERP software, please visit this section.
-
How long does it take to implement a new Manufacturing ERP system?On average, implementing a new manufacturing ERP system can take 3 to 9 months. However, the exact duration can vary widely depending on several factors: Company size and complexity Scope of implementation (full system vs. specific modules) Level of customisation required Preparedness of the organisation Chosen ERP system and vendor Hence, it's better to have a well-planned implementation strategy beforehand to avoid disruptions to your business.
-
How much does manufacturing ERP cost?The cost of manufacturing ERP varies significantly based on several factors: Company size and number of users Chosen deployment method (cloud-based vs. on-premise) Required features and modules Level of customisation Implementation and training costs Ongoing maintenance and support For a clearer understanding of ERP implementation costs tailored to your manufacturing needs, consult a professional consultancy like iTTG. We can help you navigate the complexities and ensure you make an informed investment that aligns with your business goals. Contact us today!
Epicor Features for the Industry
-
Is Epicor’s cloud accounting system used in Malaysia?Absolutely! Epicor’s cloud accounting system is widely adopted by Malaysian businesses due to its flexibility and scalability. At iTTG, we customize Epicor to align with your business workflows, ensuring full integration of financial data and processes across different departments, such as sales, purchasing, inventory, and warehousing—all securely managed in the cloud.
-
How long does it typically take to implement Epicor ERP?Implementation time varies depending on your business size and complexity. However, with iTTG Consultancy's expertise, most small to mid-size manufacturers can expect full implementation within 3-6 months. We'll provide a more accurate timeline after assessing your specific needs.
-
What kind of return on investment (ROI) can we expect from implementing Epicor ERP?While ROI varies, many of our clients report significant improvements within the first year. These include reduced operational costs, increased productivity, better inventory management, and improved financial accuracy.
-
What is a cloud-based accounting system?A cloud-based accounting system is an online platform hosted remotely, allowing multiple users to access, update, and manage all financial data in real time. This ensures data accuracy and provides a clear, up-to-date view of financial status. With a cloud-based accounting system, businesses can streamline and automate their financial processes, reducing mundane data entry and minimizing human errors.
-
Is Epicor cloud accounting system available for e-invoicing in Malaysia?Yes! At iTTG, we customized the e-invoicing feature in Epicor’s cloud accounting system, specifically designed for Malaysian businesses of all sizes and industries. We ensure the e-invoice solution meets the regulatory requirements set by LHDN, allowing businesses to submit invoices to the LHDN portal with a single click. Send us your inquiries today!
-
How can Epicor ERP improve financial management processes?Epicorcloud ERPstreamlines your financial operations by automating key processes, providing real-time data visibility, and integrating all financial aspects of your business. This leads to improved accuracy, faster reporting, better cash flow management, and more informed decision-making.
-
What training does iTTG Consultancy provide for our team during and after implementation?We offer comprehensive training programs tailored to different user roles within your organization. This includes hands-on system training, process workshops, and documentation. Post-implementation, we provide ongoing support and additional training as needed to ensure your team maximizes the benefits of Epicor ERP.
-
How does Epicor WMS enhance labor efficiency in Malaysia?With features like automated pick-pack-ship processes, Epicor WMS helps minimize manual labor dependencies, reduce human errors, and enhance overall worker productivity in warehouses in Malaysia.
-
What are the key benefits of implementing WMS for businesses in Malaysia?Implementing WMS helps Malaysian businesses enhance warehouse efficiency by optimizing inventory management, streamlining order processing, maximizing space utilization, and accurately tracking goods across the supply chain. This leads to reduced costs, improved customer satisfaction, and better decision-making.
-
What's the difference between WMS and ERP?WMS: A standalone system focused solely on optimizing warehouse operations like inventory management and order fulfillment. It lacks of additional functionality of an ERP system ERP: An all-in-one business solution that centralizes multiple functions, including warehouse management, sales, purchasing, finance, and more into one single platform, providing comprehensive operational oversight and streamlined data flow across departments. With Epicor ERP’s integrated WMS tailored to the needs of Malaysian businesses, iTTG ensures that warehouse operations are streamlined from stock receiving to delivery.
-
What is a Warehouse Management System (WMS)?A WMS, or warehouse management system, is a software application designed to manage and optimize warehouse operations in Malaysia. It helps organizations control and track the movement and storage of materials within a warehouse, from receiving to shipping, ensuring efficient operations and inventory accuracy.
-
What is ERP Software?ERP, or Enterprise Resource Planning, is a software system in Malaysia that integrates core business processes and functions into a unified platform. It allows organizations to manage and automate various aspects of their operations, including finance, human resources, manufacturing, supply chain, and customer relationship management. ERP software systems enable businesses in Malaysia and around the world to streamline workflows, improve data accuracy, and make informed decisions based on real-time information.
-
What services does iTTG Consultancy offer?iTTG Consultancy offers a wide range of services, including ERP software consultation, implementation, and support, with a special focus on Epicor ERP systems. As Epicor ERP consultants in Penang, we provide tailored solutions for warehouse management, supply chain optimization, and cloud accounting systems.
-
Why choose Epicor ERP?Epicor ERP software is known for its flexibility, scalability, and ability to support complex business processes. It is designed to enhance productivity, streamline operations, and improve overall efficiency, making it an ideal choice for businesses looking to optimize their operations and drive growth.
-
How can I make an appointment with iTTG Consultancy?To make an appointment with iTTG Consultancy, simply contact us through our website, email, or phone. Our team will schedule a consultation at your convenience to discuss your business needs and how we can help you achieve your goals. Visit our Penang branches for in-person consultations.
-
Why should I hire a Cloud ERP consultant?Hiring a Cloud ERP consultant brings specialized expertise and guidance to ensure successful implementation and optimization of your ERP system in the cloud. Consultants like those at iTTG can assess your business needs, recommend the right cloud ERP solution, customize it to fit your requirements, and provide ongoing support and training. We also streamline the migration process from on-premises systems to the cloud, ensuring minimal disruption to your operations while maximizing the benefits of cloud technology.
-
Is Cloud ERP secure?Yes, reputable Cloud ERP providers implement stringent security measures to protect data. This includes encryption protocols, secure access controls, regular security audits, and compliance with industry standards and regulations. Data stored in the cloud is often more secure than on-premises solutions due to dedicated security teams and advanced infrastructure.
-
How to connect with Epicor cloud ERP consultant?To get in touch with an Epicor Cloud ERP consultant at iTTG, you can reach out through email or website contact form. Our cloud ERP consultants will get back to you shortly. Whether you need advice on Epicor ERP implementation, customization, or support, our expert consultants are here to help you optimize your business operations.
-
What is Cloud ERP?Cloud ERP (Enterprise Resource Planning) is a software solution that allows businesses to manage their core operations such as finance, human resources, manufacturing, and supply chain management through the cloud. It eliminates the need for on-premises hardware and infrastructure, offering flexibility, scalability, and accessibility from anywhere with an internet connection.
-
What are the benefits of Cloud ERP?Cloud ERP offers several advantages, including reduced upfront costs, lower maintenance expenses, automatic software updates, enhanced security protocols managed by the provider, scalability to accommodate business growth, and real-time data accessibility for improved decision-making and collaboration. Watch video: What are the benefits of ERP
-
What is the difference between Cloud ERP and traditional ERP?Cloud ERP: Deployment: Hosted on remote servers, accessed via the internet. Cost: Subscription-based, lower upfront costs, reduces IT overhead. Accessibility: Offers remote and mobile access, scalable on-demand. Maintenance: Vendor-managed updates, reduces internal IT burden. Security: Shared responsibility, robust measures by providers. Traditional ERP: Deployment: Installed locally on company servers, on-premises. Cost: Higher initial investment in hardware, licenses, and IT infrastructure. Accessibility: Limited to on-site access, scalability may require more investment. Maintenance: Internally managed updates, requires dedicated IT resources. Security: Relies on internal IT team for implementation and upkeep.
-
Epicor Project ManagementThe Epicor Project Management function offers substantial advantages to Automotive Part factories by enhancing project organization, resource allocation, and cost control. Utilizing Work Breakdown Structure (WBS) or Milestones, it enables precise task allocation and progress tracking, ensuring efficient project execution. This structured approach aids in managing resources effectively, adhering to budgets, and preventing cost overruns. Additionally, close monitoring of costs at various project stages facilitates financial oversight, contributing to improved profitability. Integration with Microsoft Office Project enhances collaboration and adaptability, further optimizing project management processes. Overall, Epicor Project Management streamlines operations, leading to enhanced efficiency and profitability for Automotive Part factories.
-
Inventory Inaccuracy and Resource ConstraintsInaccurate inventory tracking and an inability to efficiently manage resources can result in stockouts, excess inventory, write-offs, and ultimately, financial losses.
-
Missed Revenue and Opportunity Expansion in Field ServiceFailure to capitalize on revenue-generating opportunities during field service can result in missed sales, underutilized resources, and an inability to fully leverage customer relationships for business growth.
-
Inefficient Sheet Metal Fabrication and Inventory OptimizationPoor management of sheet metal dimensions and stock can lead to material wastage, increased costs, and inefficiencies in production processes.
-
Failure to Transition to a Paperless Shop FloorNot moving towards paperless operations can lead to inefficiencies, higher operational costs, increased error rates, and environmental impacts, hindering process optimization and sustainability efforts.
-
Lack of Real-Time Product Cost MonitoringWithout real-time monitoring and control of product costs, companies may face reduced profit margins, an inability to make informed pricing decisions, and challenges in responding to market price pressures.
-
Field Engineer Productivity and Customer Satisfaction IssuesInsufficient support for field engineers can decrease on-site efficiency and customer satisfaction, impacting service quality and potentially leading to a decrease in repeat business and referrals.
-
Complexity in Product Structures and Documentation ManagementFailing to manage complex product structures and associated documents efficiently can result in errors, increased time to market, and challenges in maintaining compliance and quality standards.
-
Dynamic Design Changes and Inefficient Job SchedulingNot adapting quickly to design changes or efficiently rescheduling jobs can lead to production delays, increased costs, and an inability to meet customer delivery expectations.
-
Lifecycle Cost Management InefficienciesPoor control over the product lifecycle costs can lead to budget overruns, delayed product launches, and diminished profitability, affecting overall market competitiveness.
-
Challenges with Diverse Manufacturing MethodsInability to effectively manage different manufacturing methods can cause production inefficiencies, increased waste, and higher costs, leading to decreased operational flexibility and market responsiveness.
-
Ineffective Customer Interaction and Quality ManagementInadequately managing customer inquiries and complaints can lead to decreased customer satisfaction and loyalty, negatively impacting brand reputation and long-term revenue potential.
-
Inaccuracies in Cost Estimation and QuotationFailure to provide accurate and timely quotations can result in lost sales opportunities, customer dissatisfaction, and a tarnished reputation in the marketplace.
-
Epicor MESManufacturing Execution Systems (MES) can significantly benefit a machinery factory by providing real-time monitoring and control over production processes. By integrating MES, factories can track the progress of manufacturing orders, monitor the performance and availability of machines, and ensure that quality standards are met throughout the production cycle. This system enhances operational efficiency by minimizing downtime, reducing waste, and optimizing resource utilization. MES also supports decision-making with data-driven insights, enabling managers to identify bottlenecks, improve production schedules, and adjust workflows promptly. Furthermore, it facilitates compliance with industry standards and improves traceability, ensuring that every product meets the required specifications. Ultimately, MES empowers machinery factories to achieve higher productivity, improved quality, and increased competitiveness in the market.
-
Epicor Project ManagementEpicor Project Management offers significant advantages to a machinery factory, enhancing efficiency and cost control for large-scale manufacturing projects. By employing Work Breakdown Structure (WBS) or Milestones, it enables detailed project organization, facilitating precise task allocation and progress tracking. This structured approach aids in effectively managing resources and adhering to budgets, crucial for operational success. The capability to monitor costs closely at various project stages ensures financial oversight, preventing overruns. Additionally, the feature supports non-manufacturing project management and integrates with Microsoft Office Project, improving project adaptability and collaboration. This comprehensive tool set streamlines project execution, leading to better outcomes and increased factory profitability.
-
Epicor Mobile Field ServiceA Mobile Field Service system offers substantial benefits to a machinery factory with field engineers providing onsite services. It enhances service efficiency by enabling real-time communication between field engineers and the central office, allowing for instant access to work orders, customer information, and technical documentation. This immediacy improves response times to service calls and enables on-the-spot diagnosis and resolution of issues. Inventory management features ensure engineers have the necessary parts and tools, reducing return visits. GPS tracking optimizes route planning, saving time and fuel. Moreover, the system facilitates immediate billing and feedback collection, enhancing customer satisfaction. By streamlining field operations, the factory can achieve greater productivity, reduced operational costs, and improved service quality, leading to increased customer loyalty and revenue.
-
Epicor CRMThe Epicor Customer Relationship Management (CRM) function offers a machinery factory a comprehensive toolset to enhance its customer acquisition and retention strategies. By facilitating the creation and tracking of marketing campaigns, it enables the factory to identify and target prospects effectively, transforming them into satisfied customers. The CRM's lead management system streamlines the sales process, from initial contact to final order, ensuring a seamless transition through various sales stages. Sales personnel can manage prospects efficiently, thanks to features like workflow, forecasting, and the Salesperson Workbench. This leads to improved sales territory management and accurate sales forecasts. Overall, the CRM function optimizes the prospect-to-customer lifecycle, fostering better customer relationships and driving sales growth.
-
Mixed Mode ManufacturingEpicor mixed-mode manufacturing design offers substantial benefits to a machinery factory operations. It enables seamless integration of Make-to-Stock (MTS), Make-to-Order (MTO), and Engineer-to-Order (ETO) production modes within a single ERP system. This flexibility ensures that the factory can efficiently handle standard, customized, and highly specialized machinery production. Epicor ERP provides robust tools enable real-time visibility into customer orders, inventory levels, and production schedules, facilitating dynamic decision-making to meet varying demands. By optimizing resource utilization, reducing lead times, and improving order accuracy, the mixed-mode manufacturing design enhances operational efficiency, cost control, and customer satisfaction. It empowers machinery factories to thrive in a competitive market by delivering products tailored to customer needs while maintaining cost-effectiveness.
-
Epicor Engineering ManagementThe Epicor Engineering Management function can significantly benefit a machinery factory by enhancing the precision and adaptability of its manufacturing processes. Through accurate definition of components, subassemblies, and operations, it allows for the creation of detailed bills of materials and routings, forming a comprehensive method of manufacturing. As manufacturing practices evolve, the system's ability to update these methods ensures continuous alignment with production advancements. Part revision management, supported by Engineering Change Orders (ECO), facilitates controlled updates and approvals for changes, promoting quality and consistency. Additionally, the capability to engineer alternate methods for part revisions enables customization and flexibility across different manufacturing sites, optimizing production efficiency and responsiveness to specific requirements.
-
Epicor Mobile WarehouseEpicor Mobile Warehouse provides significant benefits to a machine production factory by modernizing and optimizing warehouse management. With this solution, workers can access real-time inventory data, track materials, and streamline warehouse operations directly from mobile devices. Barcode scanning enhances accuracy and efficiency, reducing errors in material handling and order processing. By enabling quick and accurate inventory updates, order picking, and shipping, it enhances productivity and order fulfillment speed. Additionally, it improves visibility into inventory levels, enabling better demand forecasting and inventory control. Overall, Epicor Mobile Warehouse empowers the factory to operate with increased efficiency, reduced costs, and enhanced customer satisfaction.
-
Epicor APSThe Epicor Advanced Planning & Scheduling (APS) function offers transformative benefits for a machinery factory by integrating comprehensive scheduling insights and tools. By accounting for variables like production quantities, setup times, and resource capacities, APS enables precise scheduling and job completion forecasting. Its visual boards and What If Scheduling tool allow for proactive adjustments, ensuring optimal resource allocation and preventing production bottlenecks. This leads to streamlined operations, improved efficiency, and reduced lead times. Moreover, analytical reports provide critical data on resource load and job prioritization, empowering decision-makers to enhance scheduling strategies. Ultimately, APS fosters a more agile, responsive, and efficient manufacturing process, directly contributing to increased productivity and customer satisfaction.
-
Epicor Product ConfigurationThe Epicor Product Configuration function can greatly benefit a machinery factory by streamlining the customization process for Make-to-Order (MTO) products. By utilizing the Configurator Designer, the factory can efficiently manage and offer a wide array of product customizations, from colors to sizes and hardware features. This tool simplifies the sales order entry, enabling accurate capture of customer-specific requirements and ensuring precise manufacturing instructions. It enhances operational efficiency by reducing errors in production planning and material sourcing. Additionally, the automated validation of configured part numbers against predefined rules minimizes manual intervention, ensuring compliance with design standards and accelerating the order-to-production cycle.
-
Epicor Real Time CostingEpicor Real-Time Costing provides significant benefits to a machine production factory by offering immediate visibility into the costs associated with manufacturing processes. This system enables the factory to track and analyze expenses as they occur, allowing for more accurate and timely financial reporting. By understanding the exact cost implications of raw materials, labor, and overheads in real-time, managers can make informed decisions to optimize production efficiency and reduce waste. This proactive approach to cost management helps identify profitability challenges early, facilitating swift adjustments to pricing strategies or operational practices. Ultimately, Real-Time Costing empowers a factory to improve its cost control, enhance competitive pricing, and boost overall profitability through precise and dynamic financial oversight.
-
Scheduling and Machine Optimization IssuesThe need to efficiently schedule and optimize the usage of printing machines, especially when multiple job orders compete for the same resources, presents a crucial operational challenge. This issue is pivotal to avoiding bottlenecks and ensuring timely production.
-
Lack of Real-Time Product Cost MonitoringWithout real-time monitoring and control of product costs, companies may face reduced profit margins, inability to make informed pricing decisions, and challenges in responding to market price pressures.
-
Logistical Hurdles in Material TrackingMaintaining an accurate track of paper movement through the diverse stages of production is a logistical nightmare. The challenge of ensuring that each stack of paper is accounted for, and identifying its origin from specific pallets, complicates inventory management and operational efficiency.
-
Procurement and Supply Chain ConstraintsThe task of procuring paper in the necessary dimensions and quantities is a critical challenge that affects production efficiency, cost control, and profitability. Precision in procurement and supply chain management is hampered by market variability and logistical complexities.
-
Complex Cost Estimation ChallengesThe process of accurately and swiftly estimating costs for quotations poses a significant challenge due to the intricate variables involved, such as paper and ink consumption, and the intricacies of prepress and postpress operations. This complexity often results in delays and inaccuracies that can impact competitiveness and profitability.
-
Ineffective Customer Interaction and Quality ManagementInadequately managing customer inquiries and complaints can lead to decreased customer satisfaction and loyalty, negatively impacting brand reputation and long-term revenue potential.
-
Rapid Response to Production ChangesThe printing industry's demand for short production lead times necessitates a system capable of quickly communicating changes and issues between the shop floor and production planning. The transition from traditional paper-based operations to more agile digital solutions is hindered by resistance to change and the challenges of implementing new technologies.
-
Die Cut Mold Management and Quality ConcernsEnsuring the quality and maintenance of die cut molds is a significant pain point. Effective management is essential, yet challenges in maintaining, storing, and procuring high-quality molds directly impact product quality and operational efficiency.
-
In-depth Cost Calculation DifficultiesAccurately capturing the actual cost of printed materials is fraught with difficulties due to the multitude of contributing factors such as paper consumption, machine usage, labor, and transportation costs. These costs, which accumulate throughout production and logistics, make it challenging to determine the true cost of printed matter.
-
Epicor Maintenance ManagementThe Epicor Maintenance Management function provides substantial benefits to Printing & Packaging factories by enhancing equipment reliability and optimizing maintenance processes. By tracking maintenance requests and scheduling preventative tasks for equipment like printing presses and packaging machinery, downtime is minimized, ensuring continuous production. The module allows for efficient management of capital equipment, tools, and fixtures, including air conditioning units and forklifts, critical for smooth operations. With predefined schedules and meter readings, maintenance tasks are performed promptly, reducing the risk of unexpected breakdowns. Overall, Epicor Maintenance Management empowers Printing & Packaging factories to maintain equipment reliability, minimize downtime, and optimize production efficiency, ensuring sustained operational excellence.
-
Epicor Cost Estimation & Quote ManagementThe Cost Estimation & Quote Management function offers significant benefits to Printing & Packaging factories by streamlining the process of generating accurate cost estimates and managing quotes efficiently. It allows for detailed breakdowns of costs, aiding in transparent pricing and ensuring competitiveness in the market. Additionally, seamless integration with other modules enables better coordination between quoting and production processes, improving overall operational efficiency. By enabling quick and accurate generation of quotes for both standardized and custom products, the module enhances customer satisfaction and facilitates better decision-making for resource allocation and pricing strategies.
-
Epicor Time ManagementThe Epicor Time Management function offers significant benefits to Printing & Packaging factories by streamlining labor tracking and management processes. Employees, managers, and supervisors can efficiently enter, approve, and correct time transactions, ensuring accurate recording of labor hours. With daily or weekly submission options, employees can easily submit their hours for approval, while authorized approvers can review and manage time entries promptly. This capability enhances payroll accuracy and compliance with labor regulations. Additionally, reports generated from the Time Management module provide valuable insights into employee work hours and utilization, enabling effective workforce management and optimization of production schedules in Printing & Packaging factories.
-
Epicor Job ManagementThe Epicor Job Management function offers substantial benefits to Printing & Packaging factories by streamlining manufacturing processes. It efficiently gathers data from various sources to create job records and define production schedules. With tools like the Job Manager and Planning Workbench, supervisors can effectively manage job creation and resource allocation. Labor costs are accurately tracked, and real-time status updates are provided through the Job Tracker. Key reports aid in job supervision, ensuring smooth operations from start to finish. Ultimately, Epicor Job Management enhances productivity, reduces errors, and improves overall efficiency in Printing & Packaging factories, leading to increased profitability and customer satisfaction.
-
Epicor CRMThe Epicor Customer Relationship Management (CRM) function offers significant benefits to Printing & Packaging factories by streamlining customer interactions and optimizing sales processes. By effectively managing leads and opportunities, the CRM facilitates targeted marketing campaigns, improving customer acquisition. Sales personnel can efficiently track prospects through various sales stages, ensuring seamless transitions from initial contact to final order. Features like workflow automation and forecasting enhance sales territory management and enable accurate sales forecasts. With comprehensive insights and analytics, the CRM empowers informed decision-making, driving revenue growth and fostering long-term customer relationships. Overall, it enhances efficiency, boosts sales performance, and strengthens customer engagement for Printing & Packaging factories.
-
Epicor APSThe Epicor Advanced Planning & Scheduling (APS) function offers significant advantages to Printing & Packaging factories by optimizing production planning and scheduling. By considering variables such as job quantities, setup times, and resource capacities, APS facilitates precise scheduling and forecasting of job completions. Its visual boards and What If Scheduling tool enable proactive adjustments, ensuring efficient resource allocation and preventing production bottlenecks. This results in streamlined operations, improved efficiency, and reduced lead times. Additionally, analytical reports provide critical insights into resource utilization and job prioritization, empowering decision-makers to enhance scheduling strategies. Ultimately, APS enhances agility, responsiveness, and productivity in Printing & Packaging manufacturing, driving customer satisfaction.
-
Epicor Project ManagementThe Epicor Project Management function offers substantial advantages to Printing & Packaging factories by enhancing project organization, resource allocation, and cost control. Utilizing Work Breakdown Structure (WBS) or Milestones, it enables precise task allocation and progress tracking, ensuring efficient project execution. This structured approach aids in managing resources effectively, adhering to budgets, and preventing cost overruns. Additionally, close monitoring of costs at various project stages facilitates financial oversight, contributing to improved profitability. Integration with Microsoft Office Project enhances collaboration and adaptability, further optimizing project management processes. Overall, Epicor Project Management streamlines operations, leading to enhanced efficiency and profitability for Printing & Packaging factories.
-
Epicor MESThe Epicor Manufacturing Execution System (MES) function offers substantial benefits to Printing & Packaging factories by providing real-time monitoring and control over production processes. Integration with MES enables tracking of manufacturing orders, monitoring machine performance, and ensuring quality standards throughout production cycles. This enhances operational efficiency by minimizing downtime, reducing waste, and optimizing resource utilization. Additionally, MES supports data-driven decision-making, allowing managers to identify bottlenecks, improve production schedules, and adjust workflows promptly. Moreover, it facilitates compliance with industry standards and enhances traceability, ensuring all products meet required specifications. Ultimately, Epicor MES empowers Printing & Packaging factories to achieve higher productivity, improved quality, and increased competitiveness in the market.
-
Epicor Real Time CostingEpicor Real-Time Costing offers substantial advantages to Printing & Packaging factories by providing immediate visibility into manufacturing expenses. This system allows real-time tracking and analysis of costs associated with raw materials, labor, and overheads, enabling accurate financial reporting and informed decision-making. With precise insights, managers can optimize production efficiency, reduce waste, and adjust pricing strategies accordingly. By proactively managing costs, Printing & Packaging factories can identify profitability challenges early and make swift adjustments to enhance competitiveness and overall profitability. Ultimately, Epicor Real-Time Costing empowers these factories to operate with heightened efficiency and financial transparency, ensuring long-term success in a dynamic market.
-
Epicor Mobile WarehouseEpicor Mobile Warehouse brings notable advantages to Printing & Packaging factories by modernizing and refining warehouse management. This solution grants real-time access to inventory data, enabling seamless material tracking and warehouse operations via mobile devices. Barcode scanning ensures accuracy and efficiency, minimizing errors in material handling and order processing. Swift inventory updates, order picking, and shipping enhance productivity and order fulfillment speed. Enhanced visibility into inventory levels aids in better demand forecasting and inventory control. Overall, Epicor Mobile Warehouse empowers Printing & Packaging factories to operate with heightened efficiency, reduced costs, and improved customer satisfaction, ensuring seamless warehouse management in a dynamic environment.
-
Lack of Real-Time Product Cost MonitoringWithout real-time monitoring and control of product costs, companies may face reduced profit margins, inability to make informed pricing decisions, and challenges in responding to market price pressures.
-
Difficult to Capture Production CostAccurately determining production costs in automotive part factories is challenging due to fluctuating raw material prices, varied labor costs, and complex manufacturing processes. Overhead allocation, mold and tool depreciation, and unexpected production issues further blur cost clarity. Advanced systems are vital for precise cost tracking and maintaining competitive pricing strategies.
-
Inefficient Sheet Metal Fabrication and Inventory OptimizationPoor management of sheet metal dimensions and stock can lead to material wastage, increased costs, and inefficiencies in production processes.
-
Scheduling and Machine Optimization IssuesThe need to efficiently schedule and optimize the usage of CNC machines, especially when multiple job orders compete for the same resources, presents a crucial operational challenge. This issue is pivotal to avoiding bottlenecks and ensuring timely production.
-
Rapid Response to Production ChangesThe Automotive Part industry's demand for short production lead times necessitates a system capable of quickly communicating changes and issues between the shop floor and production planning. The transition from traditional paper-based operations to more agile digital solutions is hindered by resistance to change and the challenges of implementing new technologies.
-
Procurement and Supply Chain ConstraintsMaterial procurement is a critical challenge that affects production efficiency, cost control, and profitability. Precision in procurement and supply chain management is hampered by market variability and logistical complexities.
-
Mold Management and Quality ConcernsEnsuring the quality and maintenance of molds is a significant pain point. Effective management is essential, yet challenges in maintaining, storing, and procuring high-quality molds directly impact product quality and operational efficiency.
-
Challenges with Diverse Manufacturing MethodsInability to effectively manage different manufacturing methods, for mold and molding production, can cause production inefficiencies, increased waste, and higher costs, leading to decreased operational flexibility and market responsiveness.
-
Ineffective Customer Interaction and Quality ManagementInadequately managing customer inquiries and complaints can lead to decreased customer satisfaction and loyalty, negatively impacting brand reputation and long-term revenue potential.
-
Why choose Epicor ERP Software in Malaysia?Epicor ERP software is known for its flexibility, scalability, and ability to support complex business processes in Malaysia. It is designed to enhance productivity, streamline operations, and improve overall efficiency, making it an ideal choice for businesses looking to optimize their operations and drive growth.
-
What services does iTTG Consultancy offer?ERP, or Enterprise Resource Planning, is a software system in Malaysia that integrates core business processes and functions into a unified platform. It allows organizations to manage and automate various aspects of their operations, including finance, human resources, manufacturing, supply chain, and customer relationship management. ERP software systems enable businesses in Malaysia and around the world to streamline workflows, improve data accuracy, and make informed decisions based on real-time information.
-
Which ERP Software in Malaysia is suitable for large enterprises?Large enterprises looking for scalability and streamlined operations may find Epicor better than any other ERP software in Malaysia due to its scalability, flexibility, and centralization features.
-
What is ERP software in Malaysia?ERP, or Enterprise Resource Planning, is a software system in Malaysia that integrates core business processes and functions into a unified platform. It allows organizations to manage and automate various operations, including finance, human resources, manufacturing, supply chain, and customer relationship management. Epicor is one of the best ERP software in Malaysia and around the world, which many businesses trust and choose. Epicor ERP software streamlines workflow, improves data accuracy, and makes informed decisions based on real-time information.
-
How can I make an appointment with iTTG Consultancy?To make an appointment with iTTG Consultancy, simply contact us through our website, email, or phone. Our team will schedule a consultation at your convenience to discuss your business needs and how we can help you achieve your goals.
-
How much does ERP Software cost in Malaysia?The cost of implementing ERP software in Malaysia varies depending on factors such as the modules you have chosen, the customization level, required enhancements, and the number of users. Our pricing is tailored to meet your business needs, combining subscription services with professional support. Contact us today for a personalized quote crafted just for you. Get your quote now!
-
How is ERP useful in the manufacturing industry?Implementing ERP software in the manufacturing industry can transform operations, drive business growth, and ultimately increase profitability. Here are some key advantages: Provides end-to-end visibility Improves operational efficiency Enhances inventory management Facilitates financial management Fosters collaboration between different departments For more information on the benefits of implementing manufacturing ERP software, please refer to this section.
-
What features should I look for in a manufacturing ERP system?Key features to consider in a manufacturing ERP system include: Cloud-based system Supply chain management Warehouse management Financial management Project management Customer relationship management (CRM) Enterprise performance management (EPM) Production planning and scheduling Inventory management Quality control Shop floor control Bill of materials (BOM) management Capacity planning Demand forecasting Real-time analytics and reporting Mobile accessibility Integration capabilities with other systems Compliance management Customisation options However, if you're uncertain which ERP features best suit your business needs, consider consulting ERP professionals like iTTG. These experts can provide valuable insights into ERP systems that align well with your manufacturing business requirements, helping you make an informed choice for your organisation's future.
-
What are the trends in the manufacturing ERP system?Here are some of the key trends in ERP software for the manufacturing industry nowadays: Adoption of Industry 4.0 technologies Smart manufacturing and the rise of customisation Sustainability and green practices Enhanced supply chain resilience Cloud-based ERP and remote operations Artificial intelligence and machine learning integration To learn more about these trends and innovations in manufacturing ERP software, please visit this section.
-
How long does it take to implement a new Manufacturing ERP system?On average, implementing a new manufacturing ERP system can take 3 to 9 months. However, the exact duration can vary widely depending on several factors: Company size and complexity Scope of implementation (full system vs. specific modules) Level of customisation required Preparedness of the organisation Chosen ERP system and vendor Hence, it's better to have a well-planned implementation strategy beforehand to avoid disruptions to your business.
-
How much does manufacturing ERP cost?The cost of manufacturing ERP varies significantly based on several factors: Company size and number of users Chosen deployment method (cloud-based vs. on-premise) Required features and modules Level of customisation Implementation and training costs Ongoing maintenance and support For a clearer understanding of ERP implementation costs tailored to your manufacturing needs, consult a professional consultancy like iTTG. We can help you navigate the complexities and ensure you make an informed investment that aligns with your business goals. Contact us today!

Cost Estimation